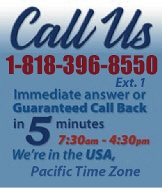 |
|
|
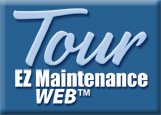 |
|
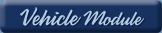 |
|
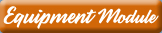
|
|
|
|
|
|
|
|
|
|
|
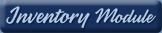 |
|
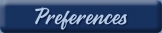 |
|
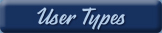 |
|
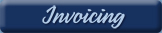 |
|
EZ Maintenance for Windows |
|
EZ Maintenance™ is also
available as a Windows's
program for the user seeking
a flat priced maintenance
software solution.
|
|
 |
Partial Client List |
|
EZ Maintenance™ for Windows
|
EZ Maintenance™ WEB |
|
|
|
Features |
|
- Schedule All Maintenance
- Equipment & Vehicles
- Full Inventory Control
- P.O.s, RFBs, Invoices
- Work Orders, Bar Coding
- Emergency Work Orders
- Email Alerts
- QuickBooks Link
- Send Work To Vendors
- Customer/Vendor Tracking
- Track Customers
- Maintenance Histories
- Access Passwords
- Supervisory Control
- And Much More!
|
|
Contact Information |
|
Pinacia Inc.
5699 Kanan Road, #349
Agoura Hills, CA USA 91301
Phone: (818) 396-8550
Sales Support: ext. 1
Tech Support: ext. 2
Fax: (818) 396-3524
info@pinacia.com
|
|
|
|
|
|
Equipment Setup
Details |
Equipment
Names allow you to quickly sort and find equipment by
category. First, enter general Equipment Name categories.
Then enter specific equipment items under the general
category. For example, a general category Equipment Name
could be "Computer"; then, each and every individual
computer will be entered & listed under the general
"Computer" category.
|
Equipment
Classification allows you to quickly sort and find equipment
by physical location. For example, your company may have
a main office, a factory, and a storage location or have
equipment located at various client site locals. You can
list outside customers by individual company names, i.e.
"Joe's Corporation", to sort and locate all
equipment at his specific company.
|
Maintenance
Types lists time intervals when maintenance is to be performed
on equipment. These types will be as varied as your needs
from daily inspections, to 30-day maintenance to Overhaul
and so forth. The Maintenance Types are used when scheduling
maintenance for particular equipment pieces and when creating
Work Orders.
|
Materials
data setup is a comprehensive list of the various parts
actually used in maintaining the equipment. Materials
could include belts, bearings, bulbs; you name it. The
data fields allow for entering specific Material Numbers
along with short descriptions. Later, the entered Materials
will appear on future drop down menus.
|
Parts
setup is a unique way to track the maintenance and wear on an idividual
part. For
example, a motor in the machine press may need a separate maintenance
schedule than
the press itself. EZ Maintenance Web allows you to track the maintenance of
individual
parts of pieces of equipment. These parts also impact on your inventory, if
you are
using the inventory module of the application.
|
Operations is
an area where you can enter the actual procedures required for equipment
maintenance. You can detail every process to do an overhaul here in
Operations. These operations are used in setting up Profiles and will be
used in the creation of work orders.
|
To
create a new Maintenance Profile, click New. (For demonstration
purposes, the screen you see here has data previously
entered). Begin by choosing the Profile Name and then
describe it in detail in the Description area. This 'snapshot'
screen lists all maintenance, (including recurring), that
needs to take place, the number of days in between each
maintenance, and finally when the maintenance is due.
Later when maintenance is due, EZ Maintenance will alert
you with a 'pop up' on the Maintenance Due screen; when
completed, it automatically reschedules itself!
|
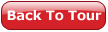 |
|
|
|